Perforation design
Wiki Write-Off Entry | |
---|---|
![]() | |
Author | Sulaiman Ureiga and Amr Almadani |
Affiliation | Saudi Aramco |
Competition | 2021 Middle East Wiki Write Off |
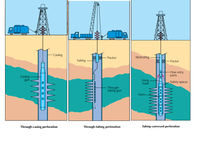
Perforation is a process that is usually conducted in the petroleum and gas industry. It is defined as the process of punching holes through the well’s casing in expectation of connecting the well to the reservoir. Usually the pay zone or interest zone is the target for perforation. This will allow the communication of fluids to form between the wellbore and pay zone. In this topic, there are many factors to be considered in order to have a successful perforation operation. Those factors would be the type of guns, conveyance methods, and the effect of perforation on the wellbore. This paper will summarize the topic with illustrations and figures.
There are three types of conveyance methods. The first method is through casing perforation. The second method is through tubing perforation, and the third method is tubing conveyed perforation (Figure1).
Perforation definitions[edit]
- Big hole charges: Prioritize hole size over penetration depth.
- Booster: An explosive that creates a path between detonator and cord.
- Carrier: A steel tube that carries the charges and protect them from rough environment.
- Deep penetrating charge: A charge that has an advantage of focusing on increasing the depth of penetration.
- Detonating cord: It is a secondary explosive that is connected to the cord.
- Detonator: A primary explosive that can be initiated by either an electrically signal or an impact reaction.
- Drillstem test (DST): A test that detects the reservoir properties using a temporary downhole shut-in valve.
- Limited entry perforation: A restriction of perforation based on the target zone’s thickness, stresses, and number of layers.
- Primer: A secondary explosive that ensures the correct sequence of detonation
- Proppant: A material that prevents closure of fractures.
- Shaped charge: A cone that is made of metal covered by secondary explosive. Thus, accomplishing penetration.
- Underbalance: The pressure of the well pore is less than the pressure of the reservoir.
- Overbalanced: The pressure of the well pore is more than the pressure of the reservoir.
- Balanced: The pressure of the well pore is equal to the pressure of the reservoir.
- Anisotropy: a molecular physical variation in the axes.
- Skin damage: A figure that describes the formation damage that could be caused by many factors.
Types of guns[edit]
There are many types of guns and convey methods that can be utilized through the perforation operation. The type of gun’s design depends on the desired operation. Each type of gun and convey method has advantages and disadvantages. An illustration of cored components must be introduced prior to gun type section.
Cord and Charges[edit]
Charges are an important part of the perforation operation. It is made out of four (4) main parts. These parts are liner, explosive, case, and a detonating cord, as shown in Figure 2. The liner is commonly made from copper, lead, and tungsten. After the explosion it turns into powder. Thus, it won’t plug the perforation hole. 42֯ is the optimum angle that would affect the length and diameter of the shots. After the shots have been detonated, the shape of shots will deform. Figure 3 illustrates core shape changes with detonation stages.
Guns classifications[edit]
There are two main kinds of guns; a hollow carrier and exposed. Both key types could be utilized through a wireline. The difference between these two guns is the gun system. Expendable and semi-expendable are two categories that fall under the exposed type of guns. These guns usually leave debris downhole after usage. Semi-expendable guns can recover their mounting unlike expendable. The exposed guns have a deeper and larger penetration rate compared to the hollow guns. The size of the exposed guns supports an optimal angle for shots (phasing). Thus, allowing for more shots per foot (shot density). As for the hollow guns, it leave no debris within the tubing.
There are four subtypes of hollow guns.
- Scallop guns: Shoot throughout the dished areas of the carrier, and utilized when debris are not accepted
- Port plug guns: This kind is used for deep penetration with a density of four shots per foot
- High shot density guns: Used in the sandy formation to provide a larger perforation hole.
- HEGS high-efficiency guns: Can be used in shallow formations. It can withstand 210 ֯F and 4,000 psi. Moreover, HEGS is faster to operate.
Perforation design[edit]
There are two main factors that could affect the flow efficiency of perforated intervals: gun selection and the differential pressure between reservoir and wellpore. To determine the entrance hole dimeter, shot phasing, and other significant factors, a correct gun design must be decided. Furthermore, it is always favored to have an underbalance operation for less skin damage (formation damage). Moreover, the permeability anisotropy is one of the main factors that affects the reservoir flow property. One common case of using guns with high density is due to the fact that vertical permeability is lower than the horizontal permeability. Building a fracture network can increase productivity tremendously. Thus, having a deeper penetration length can increase the chances of having an effective connected network. The depth of penetration also depends on rocks’ stress levels. The reservoir’s rock strength has a range from 0 to 25,000 psi.
Figure 6 illustrates the relativity and importance of geometrical shapes. The scaling system is from 1 to 4. Where 1 is at most important and 4 is the least important. To have the best perforation design, a consideration of tradeoff must be taken. Moreover, phasing is considered important when natural fracturing exists.
The downhole conditions are always used to calculate the design parameters for any type of guns and charges. Moreover, skin damage (formation damage) can heavily affect the flow regime of the reservoir. There are multiple kinds of skin damage such as wellbore damage, perforation damage, and partial penetration damage. One of the reasons that could cause skin damage is invasion caused by the mud filtrate and cement fluid loss. To improve the productivity, the perforation length must exceed the damaged wellbore zone. Achieving that will improve the skin factor.
Figure 9 shows the effects of perforations. The right image is the undamaged rock formation. The picture on the left shows the effects of perforations on the rock formation.
Summary of Natural Completion Flow Chart[edit]
In a natural completion, the most critical consideration is whether to select overbalance or underbalance perforation. If improvement in the well cleanup from underbalance perforation is significant to warrant operational complexity, then the underbalance method is preferable. However, if the technique does not yield such an advantage, overbalance perforation becomes the most viable method.
Once operators select to perforate underbalance, they should select the type of guns required in the exercise. Tubing-conveyed perforating (TCP) guns are used when there is sufficient rathole size for dropping the guns. It is especially essential during subsequent remedial operations. Through-tubing guns become relevant when such provisions are unavailable. Production and drillstem tests are essential if TCP is to be used. Production test determines whether the option of gun retrieval is needed or not. If yes, operators must stab guns through a permanent packer. However, if the option of gun retrieval is unnecessary, then running guns below the production packer become sufficient. Guns and packers can be operated on wireline, if assembly weight allows it. When operators choose overbalance perforation, they should also select the correct high shot density gun for compatibility with downhole restrictions. However, casing guns become necessary if they cannot realize such an advantage. Operators can use high-efficiency gun systems (HEGS) or port plugs.
Summary Stimulated Completion Flow Chart[edit]
The choice of underbalance or overbalance perforations methods depend on whether or not the walls of the well require stimulation. If the process is necessary, perforating underbalance is more appropriate, while perforating overbalance is relevant if such demands do not exist. Once operators select overbalance perforation, it is crucial to use through-tubing guns. it is at most critical stage, if the perforation is accomplished through work string. If the guns or the charge debris might not pose a challenge to downhole equipment, the diameter of the scallop needs correction. Otherwise, operators can use exposed guns if the downhole tools may not be affected by the debris. If a work string is not necessary for perforation, and stimulation might not benefit from high shot density, then casing guns are more appropriate. The type of casing guns used is determined by the need for limited entry perforation. Port plug guns are employed when the pressure in the wells exceeds 4,000 psi, and the uniform and circular entrance are not a high priority. HEGs are suitable when the pressure in the walls is below the limit. The electric system becomes relevant when uniform and circular entrance holes are a high priority.
Summary Sand Completion Flow Chart[edit]
If well clean-up from an underbalanced perforation justifies added complexity of sand control completion, the method is selected. A drillstem test, becomes necessary if downhole pressure or flow measurements are required. Otherwise, surge preformation should be conducted in the absence of such requirements. Regardless of the preferred tests, it is critical to determine if a significant amount of sand production might occur. If this problem might occur, operators should select a gun of reduced diameter. This can minimize the risk of gun sticking. However, in the absence of such danger, high shot density guns are recommended. Overbalance perforation becomes more appropriate if the complexity resulting from the use of underbalance perforation is not justifiable. The next stage involves selecting high shot density guns for casing size. TCP firing system and accessories are appropriate if the well's angle deviation is more than 60o. However, wireline-conveyed guns are suitable if the angle is less than 60o.[1]